Sustainability Report 2020
Who We Are
COVID-19 PANDEMICS MANAGEMENT
The Covid19 pandemics has revolutionized not only our daily lives but also the world of work. The companies had to redesign their organization and processes with the aim of preserving employment levels and ensuring working environments in which resources felt safe. We talked about it with Ermanno Zoino, AU of Prima Components Gricignano and Marco Micheli, AU of Prima Components Italia.
The start of pandemics caught everyone unprepared, which element in particular turned out to be complex to manage in the first few weeks?
«The first weeks of emergency saw several DPCM emanation in few days and each of these involved an organizational revolution: as mechanics, we had to disassemble the organization and reassemble it in a new way».
What did all this mean for a diverse reality like PSC?
«Each plant, regardless the industry sector being the same, is different in structure, number of employees, size, processes involved and hosting area which expresses its resources. We had to work on single plants regarding the general provisions laid down in the protocol drawn up in March 2020, as amended and supplemented, following a confrontation with the involved social partners».
From a practical point of view, how did this operation take shape?
«It was conducted by a specific working group for each site, in which also a doctor was part of this process, along with the plant manager and the workers’ representatives. Equipped with self-certification to be able to access the plants – a real innovation – we have modified the workplaces by simulating the presence of people. There was also a huge effort to involve the social partners and trade unions, in particular, in a context where people were lost».
Now it is possible to look forward to that stage, but at the beginning what problems arose?
«We simply did not know what kind of masks to use and where to find large quantities. All this in the constant need to ensure a supply chain to realities located in countries where pandemics arrived a little later; our customers were supportive, but still demanded the components agreed. At the same time we had to make sure that fear did not spread, despite reports being dramatic».
So, the first few months were the most complex ones?
«Yes, from mid-March to the end of April 2020 we had to stop production lines; The attempts to restart at the end of this period made us as newborns taking their first steps in a place historically belonging to us and that somehow had suddenly become new. The months of May and June, despite being characterized by low production volumes, allowed us to break in the new organizational system».
A crisis also brings with it unexpected opportunities; what happened after this first stage?
«In the second half of 2020, production was even higher than in the past: in July, we were so proud that an organization which was supposed to slow down by these new rules, including staggered shifts, did better than in the past. Overall, Covid19 gave us the opportunity to review our organization in a self-critical way».
From a practical point of view, which aspects of the organization did you have to rethink?
«We proceeded with cultural campaigns on public transport, in order to discourage traveling together and for those who could not avoid it we demanded always to wear the mask. Then we revolutionized the system of using common areas and sanitizing plants, by limiting or banning the use of changing rooms. Also the setting of refectories and canteens has been modified with the introduction of glass shield panels and other measures that help to limit the spread of the virus».
Have you faced particularly complex moments?
« Mixed feelings having an intense emotional impact. Also for this reason we have created safety protocols that go beyond what we were asked for by DPCM ».
And what were the results of such strict protocols?
«First of all, a percentage of those infected in the company far below the national average. We have to keep in mind that most of the infections happened outside the company. However,we can say that, as statitics prove, the protocols have had a positive effect».
In the early months of the pandemics, it was also very difficult to get a swab; how did you organize this?
«During the first months we have successfully organized ourselves: in Gricignano plant we provided molecular tests on a voluntary basis; in the other sites, instead, we have organized campaigns of rapid antigenic swabs, typically on a weekly basis».
And what was the response?
«It depends on the site: in some of them it was “Bulgarian”, in others we barely reached 50% of the staff. But we know that on behalf of the Group there are substantial investments to ensure the security of resources: we are talking about tens of thousands of euros per week only for tampons».
What characteristics of the company allowed to overcome this period?
«We are a Group that gives flexibility and speed of reaction, which is a fundamental feature of its DNA. Such feature is used in oder to to make of it the utmost expression.Resilience and vividness are other characteristics belonging to us also by definition, since we produce plastic components».
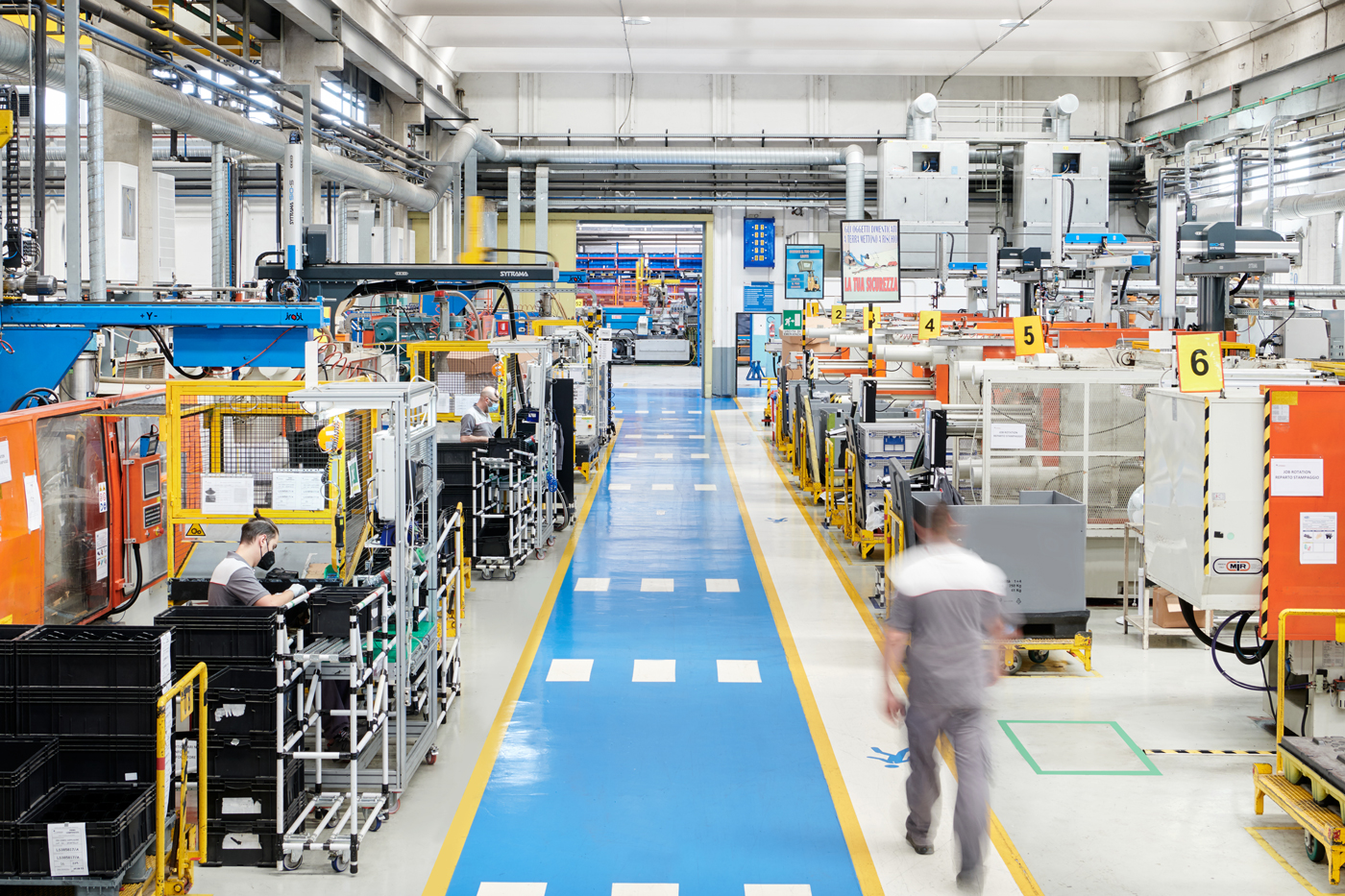
IDENTITY, VISION, MISSION AND VALUES
Identity and vision
Prima Sole Components (PSC- Stock Company)is a Group which has been operating since 1973 in the field of automotive plastic components, motor vehicles and household appliances. It designs, manufactures and sells innovative and sustainable products whose goal is to live up to its customers expectations on a regular basis. An ambitious goal, pursued thanks to a long-term and flexible partnership, where competitiveness, quality and service achieve high standards, alongside staff work of its own resources that daily carry out their activities with motivation and efficiency and constant research of revolutionary solutions that are sustainable at the same time.
PSC aims to emerge in the Italian and International market as a global actor in its operating field. Europe, Brazil, United States of America and Far East: these are the countries in which PSC is particularly reinforcing its leadership in the market of plastic components, where success is determined by three main factors:
- Competitiveness; - Innovation; - Globalization.
In order to become partner of the most prestigious customers it is fundamental to reach specific economic standards. For this reason, as well as to improve the highest degree of competitiveness, in 2018 PSC introduced COBOTs: these are collaborative robots representing industry 4.0, useful in particular for manufacturing processes, such as assembling and polishing, where human-machine interface can be incredibly handy; moreover, object of study are different applications of a world which has increased remote connections through technological Champion1
Mission
It is the Group’s intention to strengthen the relationship of trust with all stakeholders and to pursue the objectives by harmonizing each player’s interests, in compliance with the provisions of law and the principles of impartiality, reliability, loyalty, fairness and transparency. It is in this context that the objective of a shared prosperity promotes the well-being of the territory, thanks to PSC activities.
The mission of the Group is characterized by three aspects that are inseparably related to each other:
- Economic. The management of the Group is characterized by the creation of value for shareholders in compliance with rigorous economic and financial sustainability parameters.
- Productive and Market. PSC designs, manufactures and promotes innovative and Technologically advanced products that fully meet our customer’s needs.
- Social. The PSC Group is aware of the centrality of its social role towards the internal and external community, whether it local, national orinternational. For this reason, it is committed to the establishment of innovative paths aimed at improving all the Group stakeholders’ quality of life, with utmost respect for the surrounding external environment.
1 The Champion is an internal position in the Group employed in Research and Development department, qualified for a specific technology.
Values
The group takes some values which take shape within its staff’s behavior, working both individually and collectively:
- Always act with honesty and moral integrity
- Being critical with yourself and questioning how to improve yourself
- Be respectful towards the organization, highlighting meritocracy
- Focus on growth and its long-term sustainability
- Pay attention to safety and the environment
- Be respectful towards customers
The annual publication of the Sustainability Report contributes to such values consolidation and confirms the attention to the most up-to-date national and international regulations, already firmly at the basis of PSC’s working practices.
Among the values that guide the Group’s activities, two in particular have a prominent role: respect for the person and for the environment. For this reason, in the Ethical Code – updated throughout 2020 – the support and respect for human rights are clear, in accordance with the UN’s Universal Declaration. The organizational and management model, in accordance with Legislative Decree 231, was reviewed and implemented during 2020, according to the reorganization of the Group occurred over the years. In both documents, the introduction of new contents, developed on the basis of the process performed by PSC through a better sustainability of its activities, has been introduced. Such model shall be finally introduced within June 2022 in all Italian plants. Within such date the Code of Ethics will be spread in all the business units of the Group.